The Market Application & Technical Requirements of Precipitated Barium Sulfate
- Camille W.
- Mar 8, 2023
- 5 min read
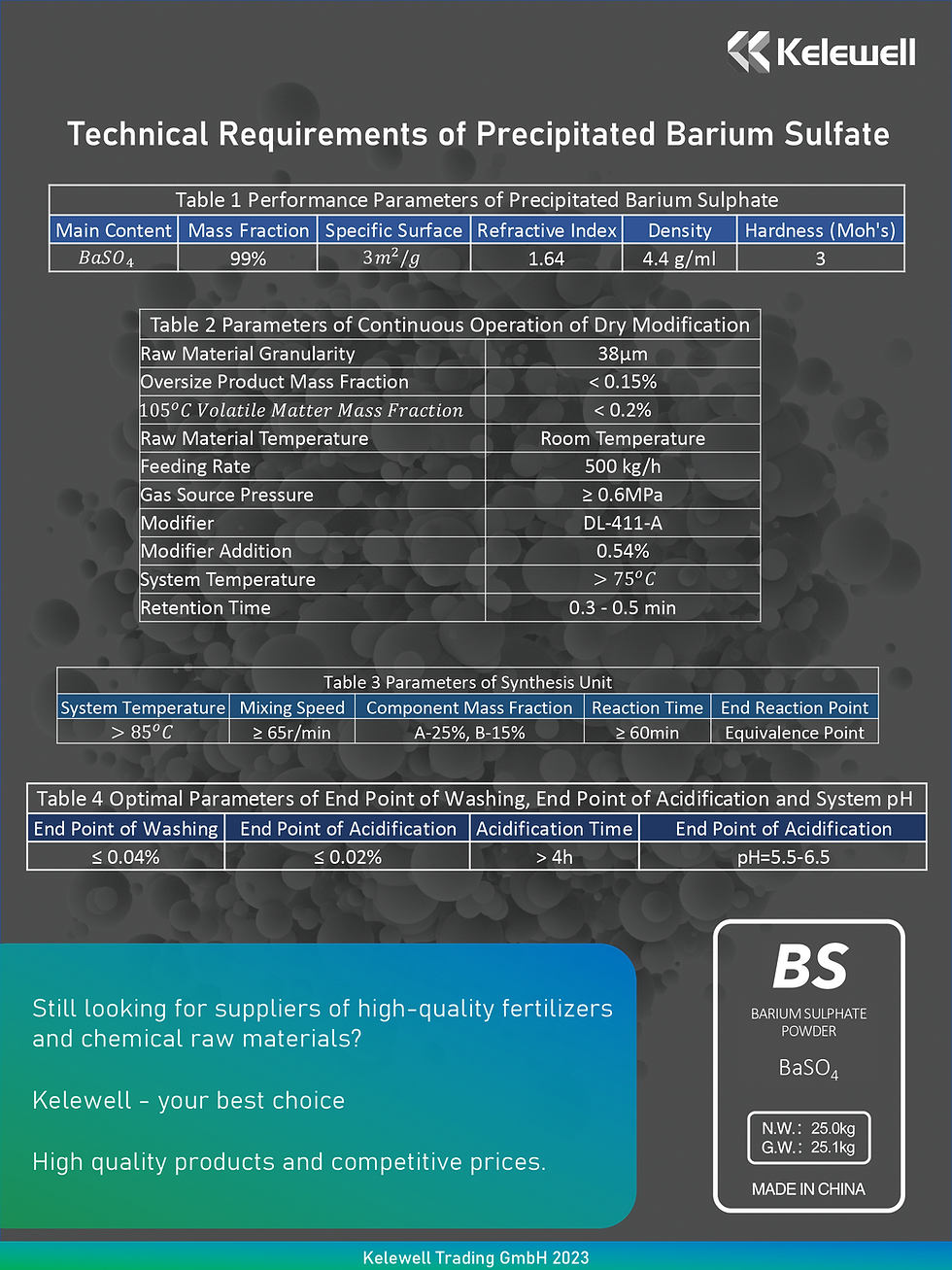
Precipitated barium sulfate is a basic raw material in chemical production, which can be used in the production of paints, plastics, rubber and ink, etc. It can also be used as a filler, which serves to defoam and improve the gloss of products. In addition, precipitated barium sulfate can also be used in the porcelain, fuel and textile industries, and is an indispensable raw material for chemical production, thus establishing its important position in the market and presenting high technical requirements. In the practical application of precipitated barium sulfate, to meet the technical requirements, unit process control is required, and it is recommended to use wet modification and dry modification, etc.
1 - Application of Precipitated Barium Sulfate
Precipitated barium sulfate has different roles in production applications respectively, which are summarized as the following four points.
1) As a high-quality filler. Precipitated barium sulfate is applied in the production of engineering plastics, and its filler mass fraction can reach 10%-28%, which is conducive to the optimization of aging resistance, wear resistance and mechanical properties.
2) As a paint filling material. Precipitated barium sulfate can be used in the production of wood paint, varnish and ship's thick paint, etc. Because of the strong chemical resistance, it is used in the production of high-gloss topcoat, which is beneficial to improve the weather resistance, optimize the flow state of paint and paint film strength, and strengthen the stability of color.
3) As an exterior wall coating. Precipitated barium sulfate is an important filling material in exterior wall paint, which can strengthen the light resistance and weather resistance of the paint and be applied in practice to avoid quality problems such as cracks and wrinkles and extend the service life. At the same time, precipitated barium sulfate can also be used as a raw material to produce emulsion paint, whether it is used for home interior decoration or factory workshop environment decoration. If applied in powder coating, it also presents obvious advantages in filling capacity, brightness, glossiness, fluidity, pigment compatibility, etc.
4) As a printing ink filler. Because the printing ink production has high requirements for primer, and to reduce the wear rate and improve the brightness, considering the above needs, the use of precipitated barium sulfate is the best choice.
2 - Technical Requirements of Precipitated Barium Sulfate
2.1 Product Performance Control
As the performance parameters of precipitated barium sulfate shown in Table 1, the current production process in China has strictly implemented the index control, but because of the differences in the technical requirements in different applications, so the internal control indexes developed by manufacturers are often higher than the national standard value. Precipitated barium sulfate product production needs to meet the following three requirements:
Firstly, to ensure the stability of product quality, quality differences of precipitated barium sulfate production batches are strictly controlled on the basis of meeting the specifications.
Secondly, it is the process index control. To ensure the uniformity of the product batch index, the raw material liquid concentration, mixing method, reaction temperature and time in the process should be strictly controlled.
Thirdly, to determine the product grade, the more common product staging methods include technical index staging and application staging, in which, the technical index grade needs to start from the four levels of general barium, modified superfine barium, fine barium and nano barium, and the application field grade should be divided into general water-based, oil-based coatings, powder coatings, emulsion paints, engineering plastics, inks, pharmaceuticals, storage batteries, paper and other types according to the current market demand.
2.2 Product Function Optimization
Optimize the process conditions and conduct surface treatment according to the various requirements of each application area of precipitated barium sulfate, so that precipitated barium sulfate can have functionalization and specialization. If process methods are diversified, in the production of different levels of products such as 5-30μm, sub-micron and nano level, it is recommended to choose the dry and wet modification treatment to enable the precipitated barium sulfate particles to have hyper-dispersion in water and oil system.
2.3 Low cost & High yield
In the synthesis and surface treatment of precipitated barium sulfate, to improve the technologies and effectively resist the market risk, it is necessary to do a good job of cost management and improve economic efficiency.
Firstly, we should analyze the current market environment and summarize the technical requirements of users for precipitated barium sulfate as the basis for research and development with technology and parameter optimization.
Secondly, we should select the process ideas and process control means scientifically to minimize the cost input. For example, for the synthesis reaction unit of common precipitated barium sulfate, it is recommended to add modifier on the basis of the original equipment, and change the feeding mode, optimize the parameters of stirring speed and feeding concentration, etc., to obtain modified products to ensure that the particle size is less than 10μm. For the production of fine precipitated barium sulfate, the modifier can be entrained by high-pressure airflow, set the condition to 0.6MPa, and it will be applied within the airflow crushing system to ensure the dry modification process is based on d97≤3.0μm. The required cost is not high, and it meets the requirement to improve product technology.
3 - Unit Process Control Technology of Precipitated Barium Sulfate Synthesis
3.1 Wet Modification
After adjusting the concentration of modifier and preparing a solution, add it to the synthesis system according to the reaction mechanism. During reaction nucleation and crystal nucleus growth period, the modifier wraps on particle surface, or forms inhibition of nucleation and growth of the crystal (particle) during crystallization, adjusts the particle size distribution state, and optimizes the surface properties of the particles. Generally, common modifiers in the production include zirconium aluminate coupling agent, sodium 12-hydroxystearate and polyethylene oxide dodecyl amine and several other. Staff adjustment and control of reaction time, system pH, component concentration, can also achieve the above purpose.
3.2 Dry Modification
Usually, within the high-speed heated mixer, to achieve the chemical coating of the particle surface, a dry modification treatment method is used. The treatment is to adjust the impeller to a high-speed rotation state, and the particle flow into an up and down spiral movement state, and the particles will collide and rub during this period, accelerate particle dispersion, and uniformly adsorb liquid surface modifier. In the industrial production process, generally it is more common to use SLG type powder surface modifier, PSC type powder surface modifier and fluidized bed of the spray airflow mill. Precise adjustment of parameters is required, as shown in Table 2. After dry modification, particle size distribution and dispersion of precipitated barium sulfate has significantly improved. And after modification treatment, it is used as filler material in PVC production, and the synergistic effect of heat stabilization, wetting and plasticity, processing performance is optimized, and the amount of filler is increased, which effectively improves the comprehensive performance of the product.
3.3 Unit Process Control
Firstly, in terms of the synthesis unit, it should focus on the control of the primary particle size distribution state, and set the feeding method, reaction temperature and time, stirring speed and component concentration parameters according to requirements. The parameters are shown in Table 3 as from practical experience.
Secondly, in terms of the separation, washing and acidification units, the end point of washing, end point of acidification, and the optimal parameters of system pH are shown in Table 4.
Thirdly, in terms of the drying unit, the technician implements spray drying to dewater, dry and conduct wet modification of the slurry. Process control parameters are as follows:
Hot air temperature ≥ 420℃
Feed solids mass fraction ≥ 45%
Atomizer speed ≥ 15000r/min
Flow rate of 5m3/h
Capture mode: three-stage capture
105℃ volatile matter mass fraction <0.15%
Modifier temperature ≥ 75℃
Fourthly, in terms of the airflow crushing unit, through the fluidized bed equipment in the jet airflow mill, perform the physical crushing of barium, dry modification process. And the process control parameters are as follows:
Gas source pressure 0.6MPa
Bed temperature ≥ 75℃
Classifier wheel speed > 800r/min
Capture form: bag trapping
Comments