Potassium Hydroxide (KOH): The "Alkaline Engine" Driving Modern Industry
- fernando chen
- Mar 21
- 5 min read
From lithium batteries in smartphones to biodiesel in the kitchen, from pharmaceutical laboratories to photovoltaic power plants, this chemical substance is quietly driving the progress of human civilization — it is Potassium Hydroxide (KOH).
As a cornerstone of industry with a global annual consumption exceeding 2.5 million tons, potassium hydroxide uses its strong alkalinity as a “weapon” to open up a vast range of applications in both traditional manufacturing and cutting-edge technologies.
This article will provide a scientific perspective to systematically introduce the properties and uses of this "industrial all-rounder," with a special focus on the production and application fields of 90% potassium hydroxide flakes.
Basic Information and Molecular Structure: The Essence of a Strong Alkali
Name: Potassium Hydroxide
Chemical Formula: KOH
Molecular Weight: 56.11 (K=39.10, O=16.00, H=1.01)
CAS No: 1310-58-3
Main Physical and Chemical Properties:
Property | Value or Description |
Strong Alkalinity | pH up to 13.5 (1M aqueous solution) |
Thermal Effect | Releases about 57.6 kJ/mol of heat when dissolved in water |
Hygroscopicity | Absorbs moisture and liquefies within 30 minutes when exposed to air |
Melting Point | Approx. 360°C |
Boiling Point | Approx. 1320°C |
Density | Approx. 2.044 g/cm³ |
Solubility | Easily soluble in water, ethanol, and glycerol; insoluble in ether, acetone, etc. |
Product Classification: Grades and Preparation Methods of KOH
Classification by Purity Level
Grade | Purity Requirement | Impurity Control | Typical Uses |
Industrial Grade | ≥90% | Cl⁻ ≤ 0.1%, Fe ≤ 0.003% | Metal cleaning, waste gas treatment |
Food Grade (E525) | ≥90% | As ≤ 3 ppm, Pb ≤ 5 ppm | Olive debittering, cocoa processing |
Electronic Grade | ≥99.9% | Individual metal ≤ 0.1 ppm, total metal ≤ 1 ppm | Semiconductor etching solution, photovoltaic silicon wafer treatment |
Reagent Grade | ≥99.99% | Heavy metals ≤ 0.1 ppm, individual impurities ≤ 0.001% | Analytical chemical standards, pharmaceutical synthesis |
Classification by Physical Form and Preparation Methods
Solid Potassium Hydroxide
Flake KOH (Potassium Hydroxide Flakes)
Melted Cooling Process: Melted KOH (90% concentration, approx. 400°C) is transferred to a double-roller machine, where cooling water (5-10°C) cools the molten liquid into thin sheets (1-3 mm thick).
Crushing and Screening: The flake product is crushed to adjust the size and screened to produce standard flakes (10–30 mm²), with a moisture content of ≤0.5%.
Granular KOH
Spray Granulation: Melted KOH is atomized into fine droplets (2–5 mm in diameter) by high-pressure nozzles and cooled in a tower by air.
Surface Modification: Add 0.1–0.5% magnesium stearate as an anti-caking agent to improve flowability.
Powdered KOH
Low-Temperature Grinding: Flake KOH is placed in a -20°C environment and ground using a super-fine pulverizer (10,000 rpm) to 200–400 mesh (37–74 μm).
Inert Gas Protection: Nitrogen gas is used throughout the grinding process to prevent moisture absorption and oxidation.
Packaging: Vacuum aluminum foil bags with desiccants, moisture-proof and anti-caking.
Liquid Potassium Hydroxide
Concentration: 45%, 50% aqueous solution
Direct Dilution: 90% flake KOH is dissolved in water at a temperature of 80–90°C.
Continuous Production Process: An online mixing system monitors concentration in real-time, and a 5 μm filter removes undissolved particles to ensure clarity.
Storage and Transport: Use polyethylene (PE) or fiberglass reinforced plastic (FRP) containers, avoid carbon steel containers.
Industrial Production: The Evolution of Electrolysis Technology
Potassium hydroxide is mainly produced by electrolyzing potassium chloride (KCl) aqueous solution. The three common processes are:
Diaphragm Electrolysis
Process Description: Asbestos diaphragms separate the anode and cathode, with KCl solution electrolyzed to produce KOH and hydrogen at the cathode, chlorine at the anode.
Characteristics: Purity 45–50%, Cl⁻ ≤ 0.1%.
Application Areas: Industrial-grade cleaning agents, low-end chemical raw materials.
Limitation: Asbestos contamination risk, not suitable for food or pharmaceutical applications.
Ion-Exchange Membrane Electrolysis
Process Description: Uses perfluorosulfonic acid ion-exchange membranes to selectively pass K⁺ ions, producing high-purity KOH.
Characteristics: Purity 50–55%, Cl⁻ < 0.005%, no asbestos contamination.
Application Areas: Electronic chemicals, food additives (E525), pharmaceutical intermediates.
Causticizing Method
Reaction Formula: K₂CO₃ + Ca(OH)₂ → 2KOH + CaCO₃↓
Characteristics: Purity 40–45%, contains K₂CO₃ ≤ 3%.
Application Scenario: Laboratory, ceramic glaze preparation.
Safety and Environmental Protection Guidelines
1. Operational Safety
Strictly avoid direct contact; wear goggles, gloves, and masks.
In case of skin or eye contact, wash thoroughly with water for 15 minutes and seek medical attention.
2. Storage Guidelines
Store in a dry, cool, and well-ventilated place.
Keep away from acids and flammable materials to avoid moisture absorption and chemical reactions.
3. Environmental Impact and Treatment
Discharged into water, KOH will significantly raise the pH, causing harm to aquatic ecosystems.
Wastewater containing KOH must be neutralized with acidic substances (such as HCl or H₂SO₄) before discharge.
Industrial Applications: From Traditional Chemicals to New Energy Frontiers
Traditional Chemicals
Potassium Salt Manufacturing:
Potassium Carbonate (KOH + CO₂ → K₂CO₃), key raw material for the glass industry.
Monopotassium Phosphate (KOH + H₃PO₄ → KH₂PO₄), core component of high-end water-soluble fertilizers.
Saponification: Replacing sodium hydroxide to produce high-end liquid soap and cosmetics.
New Energy and Electronics
Alkaline Batteries: Used as 35% KOH solution electrolytes, improving conductivity in zinc-manganese batteries.
Fuel Cell Electrolyte: KOH melted and injected into porous ceramic carriers for high-temperature fuel cells (operating temperature 600°C).
Photovoltaic Industry: Used for silicon wafer etching to remove impurity layers.
Biodiesel Catalyst
Catalyzing the transesterification of vegetable oil and methanol, achieving a conversion rate of up to 98%, with about 20 kg KOH consumed per ton of biodiesel.
Other Applications
Pharmaceutical Intermediates: Synthesis of potassium penicillin salts.
Gas Purification: Adsorption of CO₂, H₂S, and other acidic gases.
Food Processing: Legal food additive (E525), used for olive debittering, cocoa processing, etc.
Market Data: Global Supply and Demand, Price Trends
Global Annual Production
Total production is approximately 2.5 million tons (2023), with the annual demand for 90% potassium hydroxide flakes reaching about 1.2 million tons (accounting for 50% of the total solid KOH consumption).
China’s share exceeds 40%, with major companies such as Qinghai Salt Lake Industry and Olin Corporation (USA).
Consumption Structure
Application Area | Share |
Chemical Raw Materials | 45% |
Cleaning Agents | 25% |
Batteries & Electronics | 15% |
Food & Pharmaceuticals | 15% |
Price Fluctuations
The average price in 2023 ranged from $800–$1200 per ton.
Prices are influenced by potassium mineral supply, energy costs, and expansion in the new energy sector.
Conclusion
Potassium Hydroxide, a seemingly ordinary chemical, bridges the gap between traditional and future industries with its remarkable alkaline properties.
The 90% potassium hydroxide flakes stand out for their high concentration and ease of storage, making them a "universal alkaline platform material" in fields like chemicals, new energy, and environmental protection. From molten flake production to precise applications, each piece of KOH encapsulates the wisdom of modern chemical engineering, supporting a vast industrial chain from basic chemicals to cutting-edge technologies, from daily cleaning to sustainable energy.
As green chemistry and new energy technologies continue to evolve, potassium hydroxide will play an increasingly vital role in driving innovation and transforming industries.
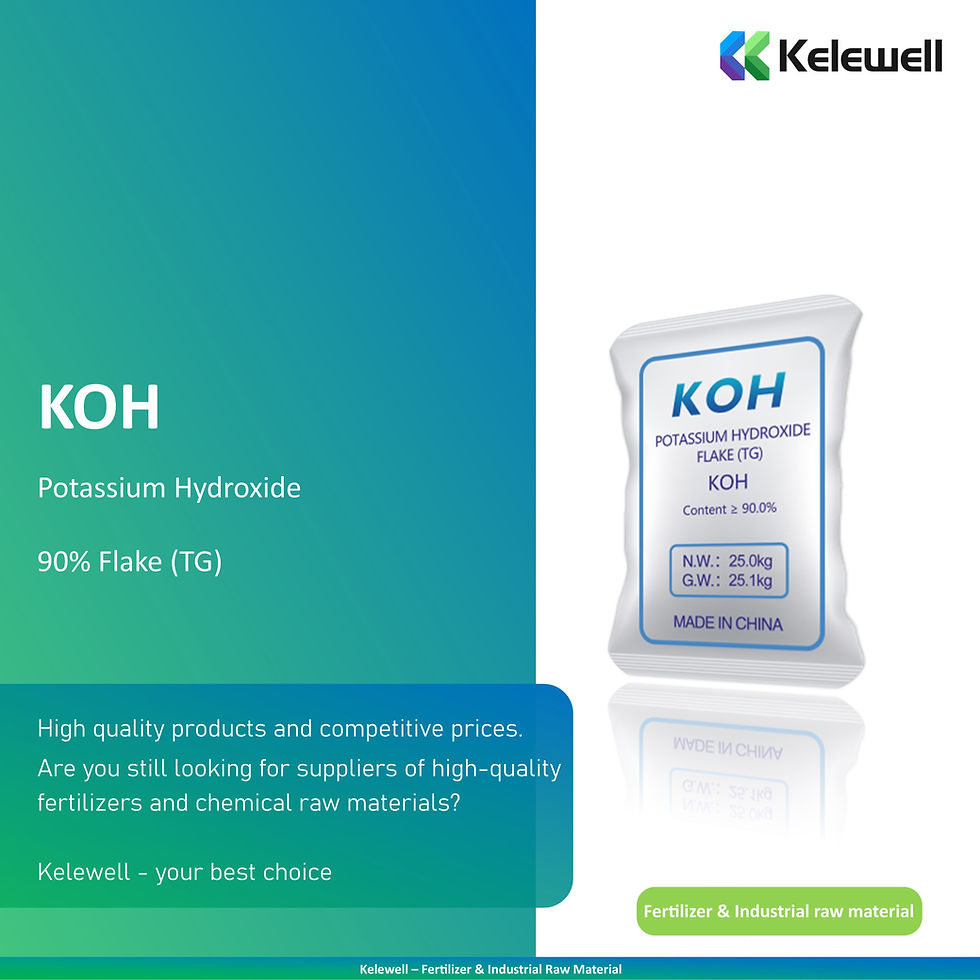
Comments